QR codes on a dairy farm
15. Oktober 2021 — General Information, Calf Feeding, Calf management, Practice report, Products — #Vocational training #Management #MilkTaxi #Practice report #QR code #SOPGrell GbR in Duvensee takes an innovative and pioneering approach to its work. Explanatory videos and less paperwork are now set to boost work efficiency and simplify processes on the farm.
This article is about
- The introduction of short explanatory videos on a farm that can be accessed via QR codes
- A special system for calf care
- A Holm & Laue 260 L MilkTaxi with pasteuriser
Keeping a close eye on your animals at all times is the be-all and end-all. Everybody has their own system – as is the case with Grell GbR in Duvensee. We talked to Knud Grell about his calf feeding and how he has taken a whole new approach with the help of QR codes.
Continuity is very important in calf feeding. For this reason, it is often preferable for as few different staff members as possible to take care of the calves. Grell GbR employs around 12 people, two to three of whom are always vocational trainees. With 550 cows to milk in Duvensee, there is a correspondingly large number of calves to take care of. Up to six of the 12 employees take care of the youngest animals on the farm. This means many different people who are all supposed to care for the calves in the same way – almost impossible without a good system.
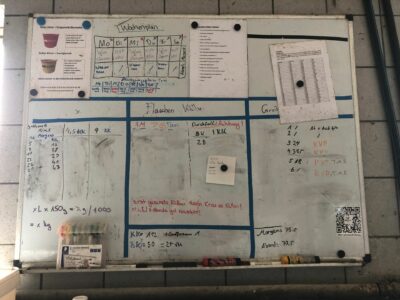
One of the things that immediately catches the eye in the GbR's milk parlour is a large whiteboard. It lists virtually all the calf feeding processes on the farm: from to-do lists and tables with mixing ratios, to a weekly bedding plan and instructions on the correct method of colostrum feeding.
In addition to the whiteboard, there is also a printed overview of all calves, where you can read the age and progress of the animals.
A kind of handout also explains all the individual steps of calf feeding in great detail, as well as common problems and their solutions.
"We want everyone who cares for our calves to always have the same level of knowledge. This is how we can work efficiently and ensure that our animals are doing well. There's also a WhatsApp group to report calves that are drinking badly or any peculiarities or incidents that everyone should be aware of.”
After just a few minutes of talking, we are very impressed at how much dedication and thought goes into the work here. However, while Knud Grell is explaining all the processes of his calf management and the records in the milk parlour, you notice a slight dissatisfaction in his expression: "All in all, the system works really well, but it's not quite there either. There's a lot of paperwork and some of the processes are far too complicated." His 260-litre MilkTaxi has already allowed him to do away with the annoying task of lugging buckets and mixing milk by hand, and now he would like to find a better solution for all the other processes as well.
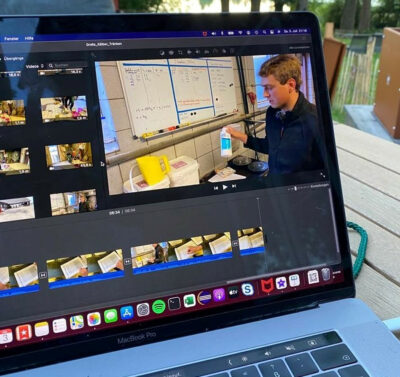
No sooner said than done! The basic idea is that a specially created QR code on the MilkTaxi allows anyone feeding the calves to access an explanatory video using a smartphone. The video provides a brief explanation of all the processes and describes what the employee needs to know. Knud put this idea together with his sister, who runs the farm's office, and a friend who knows a lot about IT. What started out as theory was soon put into practice. A detailed video on the subject was shot featuring a hard-working vocational trainee: Calf feeding at Grell GbR.
"As might be expected, the result was not a short clip after all, but a 48-minute explanatory video. This doesn't quite correspond to my basic idea, but the video is perfect for employees who have to take care of the calves again after a long time and especially for new trainees. Before everything is explained to you in person – because no technology has yet been able to replace that – you have the opportunity to gain in-depth prior knowledge from the video.”
Our Weidemann was used as a test object before the MilkTaxi got its QR code. There’s now also a brief video on how to operate the small farm loader.
What works so well in calf feeding and with the Weidemann is now to be followed in the milking parlour. There is also a recent video in which Knud Grell explains in about ten minutes how the milking routine works at Grell – it even includes subtitles in different languages.
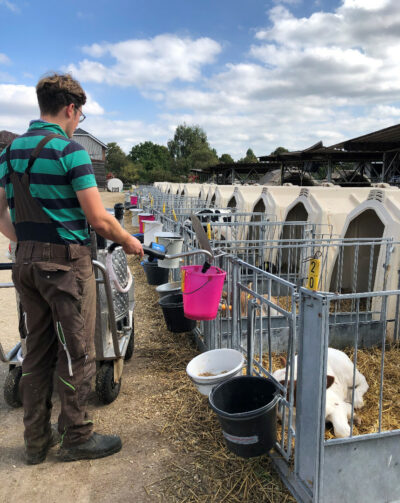
We were allowed to test the QR codes on site, watch the videos and were delighted: just hold the mobile phone over the QR code and the corresponding video plays. The content is easy to understand and explained in a very engaging way.
For the future, the farm manager hopes that many more processes and data will be digitalised and automated. "Ideally, everything comes together in one place and is easy for all employees to see and understand," Knud explains. The main focus should be on individual care and recording of data for each animal.
We'd like to take this opportunity to thank Knud for his time and the interesting conversation, and we're looking forward to seeing what he, his sister and his IT friend come up with in the future. We wish them continued success.
Let us know what you think: Are QR codes on a farm a good idea and is this perhaps the solution to training up new vocational trainees nowadays? How far are the processes on your farm already digitalised and/or automated?
Would you like to learn more about the Grell-Milch GbR?
Then have a look at their website: https://www.grell-duvensee.de/
Or leave a like on their Facebook page: https://www.facebook.com/grellmilch