The H&L whole milk story
12. November 2021 — General Information, Calf Feeding, Pasteurising, Products — #Colostrum #CalfExpert #DoubleJug #Management #MilkTaxi #Pasteurising #Calf feeder #Whole milkFeeding valuable whole milk to calves is child's play with the right concept.
Calves need lots of milk to grow! There is no question about that. However, there are a thousand different concepts as to how milk feeding should be done. As skimmed milk powder, whey powder, yoghurt, acidified whole milk, pasteurised whole milk, high concentration, low concentration, with or without supplement, … far too many options!
This article is about
- the advantages and disadvantages of whole milk feeding
- the question of availability of whole milk
- the possibilities of pasteurising
- the storage of whole milk and feeding at calf feeders
It could be that easy: we simply feed the calf what mother nature intended to feed, the milk from its mother!
However, there are many reservations about the use of whole milk for calf feeding:
- The milk is too expensive to be fed.
- It is difficult to transport and heat up whole milk.
- The cleaning effort for the feeding technology is high.
- Milk must be stored cold.
- The quality of the milk is often questionable.
- Important substances are missing (iron and vitamins).
On the other hand, there are advantages in favour of using whole milk in calf feeding:
- Milk contains a high proportion of highly digestible casein.
- High milk consumption (ad libitum) is often only possible with whole milk.
- Whole milk contains many probiotics and immunoglobulins even after the colostrum phase.
- Non-marketable milk is available for free.
- After pasteurisation, germ-contaminated milk can be fed without restrictions.
- Whole milk is available at every dairy farm.
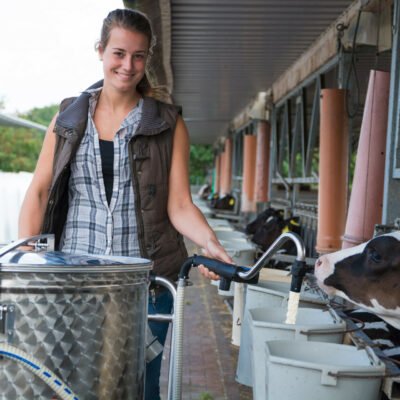
What is striking in this comparison is that it is mainly technical problems that hinder the use of whole milk in the calf barn and that, on the other hand, nutritional advantages prevail.
So if an optimum solution could be found for the the technical options of transport, germ treatment, storage and feeding, whole milk would be the perfect feedstuff for young calves.
Problem 1: Separation of “calf milk” in the milking parlour
Basically, five different sorts of milk must be separated directly in the milking parlour:
- Marketable, high-quality fresh milk.
- High-quality colostrum from the first milking. It should be collected separately and fed directly to newborn calves or it should be cooled or frozen in colostrum bags.
- Colostrum from second milking until the end of the waiting period.
- Milk contaminated with germs and cells which is not marketable. Note that milk of very poor quality – sometimes with changes in appearance – should not be used as feed even after pasteurisation.
- Milk containing antibiotics should not be used at all due to the risk of development of resistance. An inhibitor test for antibiotics can provide safety before feeding the milk.
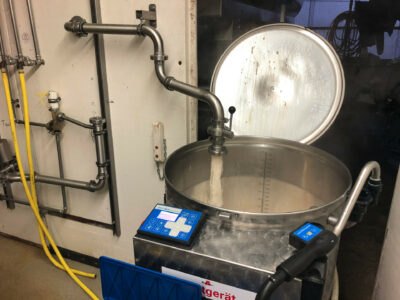
Whole milk for calves should be composed of the fractions 1) marketable fresh milk, 3) colostrum as well as some 4) moderately germ-loaded milk. This milk could be milked in the milking parlour via a second milk line directly into a separate tank or a waiting MilkTaxi. This method is standard for the milking robot, but a second milk line is often not installed in conventional milking parlours for reasons of cost.
Alternatively, collecting pits for milk could be installed in the milking parlour, into which the contents of the milking buckets are emptied and then pumped out of the milking parlour.
The first colostrum (2) should be stored separately in milking buckets and processed quickly. Unfortunately, manual work cannot be avoided here. The milk can then be filled into bags, bottles or similar, pasteurised, chilled or immediately fed after heating. There are various working routines for this such as the coloQuick management system.
Inhibitor milk (5) and milk from cows with very diseased udders (some 4) should be disposed of with the liquid manure in the milking parlour.
Problem 2: Treatment of milk contaminated with germs
As described above, sometimes milk containing pathogens is used in calf feeding. If the milk is lightly contaminated, this is not a problem if the milk is pasteurised. Pasteurisation is a tried-and-tested heating method during which the milk is sterilised. A distinction is made between two different systems:
Batch process (so-called batch pasteurisation)
The milk is sterilised at 60 - 63 °C for a period of 30 - 70 minutes (residual germ content <0.5%). This process is suitable for small and medium-sized farms that require up to 250 litres of milk per meal. It is technically relatively simple and very inexpensive. With the MilkTaxi the pasteuriser function is optionally included in the device itself.
However, the process is not very energy-efficient. All the energy that is put into the system is lost because the heat is wasted after the process.
Flash process or High-Temperature-Short-Time (HTST) process (so-called continuous pasteurisation)
In the flash process, the milk is heated to 73 °C and held at this temperature for 15 seconds. The flash pasteurisers are designed for higher performance. Calf milk pasteurisers like the MediumFrame or the LargeFrame pasteuriser pasteurise between 350 and approx. 1,500 litres per hour. With two heat exchangers the systems work very energy efficiently. They use the heat generated during pasteurisation to preheat the incoming milk so that the energy requirement is significantly lower than with the batch process. Furthermore, there is also the option of using waste heat from biogas plants or heat recovery from milk cooling. Then these pasteurisers work extremely economically and often need less energy than would be necessary to heat the milk from the storage temperature to the drinking temperature.
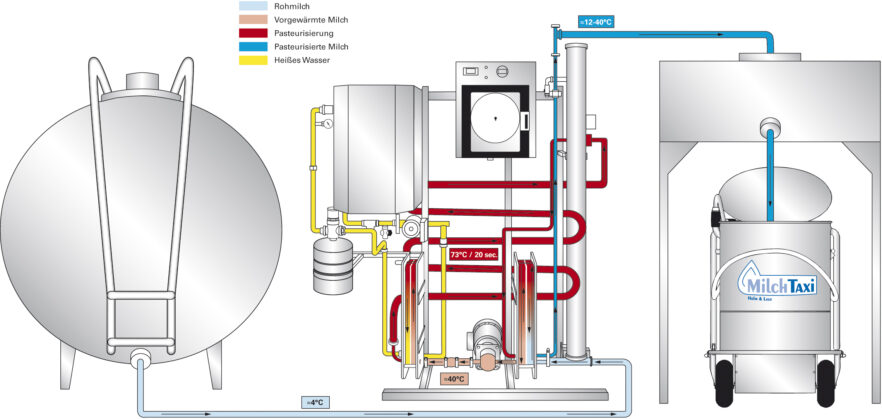
However, these systems are technically very complex because e. g. several storage tanks are necessary: One storage tank for the raw milk in which the separated milk arrives from the milking parlour, and one storage tank for the finished pasteurised milk.
The finished pasteurised milk could flow into a MilkTaxi for example. Since you can set the flash pasteurisers so that the milk enters the MilkTaxi at drinking temperature, you can start feeding the calves immediately.
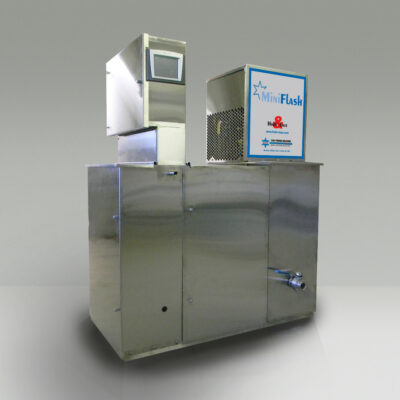
Here the MiniFlash scores highly. It has an integrated tank for raw milk with a volume of 150 or 300 litres. The tank has integrated cooling with an empty sensor, an agitator and automatic cleaning. The MiniFlash is particularly suitable for use on farms with milking robots. The automatically separated milk is simply pumped into the tank and then cooled down immediately to maintain quality.
Problem 3: Storage of the separated milk
After the calves milk has been separated off in the milking parlour, the question is how to store the milk and transport it to the calves.
The easiest way is by MilkTaxi, where the milk is stored, driven to the calves and then pumped into the drinking buckets. The flexibility of the MilkTaxi system with its wide range of options is already appreciated by tens of thousands of farms.
But when calf feeders are used, the farmer is always faced with complicated challenges. Firstly, the milk must be transported to the calf barn. If this is not far away, pipes with possibility of cleaning are certainly a good alternative. However, if longer distances have to be covered, a MilkTaxi can also be used here to transport the milk. Thus, the calves in the individual boxes could be fed first and then the storage tank at the calf feeder could be filled or the MilkTaxi itself could serve as a storage tank.
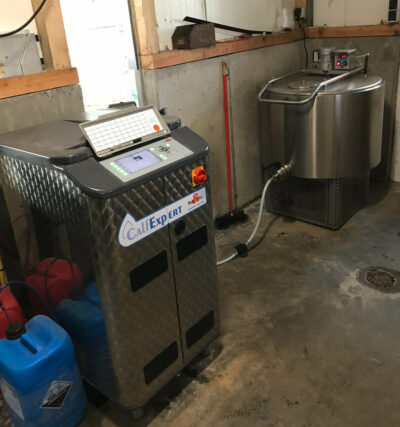
Whichever way, the storage tank at the calf feeder must have cooling so that the milk maintains its quality. Here cooling temperatures of 4 – 5 °C are not necessary if the milk is consumed within 12 hours (from one milking time to the next). Temperatures below 10 – 12 °C are then often sufficient to keep the milk fresh during this period. This higher temperature saves enormous amounts of energy, because the lower the storage temperature the higher the additional energy required for cooling and later heating.
There are basically four problems with conventional storage tanks in connection with calf feeders:
- Residual milk in the tank before refilling
The milk tank is rarely completely empty at the time of refilling. For this reason, residual quantities usually have to be filled into tanks provided and then manually fed or disposed of.
- Early emptying
The next common case is that you haven't filled enough milk into the tank and the feeder cannot feed milk for a certain time because the tank is empty.
- Ice formation at low fill levels
Milk tanks designed for the storage of fresh milk always tend to ice up at low filling levels because there is no automatic shutdown of the cooling.
- Cleaning of tank and line
The tank must be cleaned before refilling. This is usually done manually or is completely omitted when time is short. Since hygiene and cleanliness are the key to success for young calves, this quite common practice is often the cause of calf disease. In addition, the line from the calf feeder to the MilkTaxi must also be cleaned at this time. Cleaning the tank and line always means that the supply of milk diet at the feeder is interrupted for at least ¾ to 1 hour.
Modern whole milk feeding with CalfExpert and DoubleJug
In the past, all the above-mentioned problems meant that whole milk was rarely used with calf feeders. The nutritional advantages are known but the technical disadvantages outweigh them!
With the new whole milk concept from Holm & Laue, however, these problems are overcome and an efficient, cost-effective system with maximum performance is used.
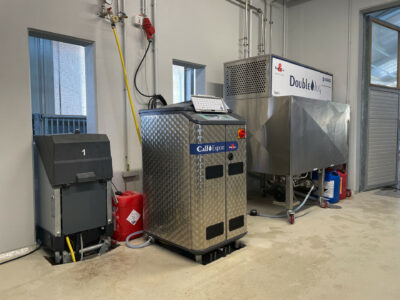
The DoubleJug is a milk tank with two compartments specially designed for calf feeders. The CalfExpert calf feeder gets its milk from one of these tanks. If this tank becomes empty the DoubleJug automatically switches to the second tank and the CalfExpert can continue feeding without interruption.
As soon as the first tank is empty, it is cleaned automatically. Then it waits to be filled again (e.g. by the MilkTaxi or via a pipe). Usually both tanks are filled to take advantage of the maximum capacity of the DoubleJug.
The advantage of the two-chamber system is that the DoubleJug can be filled at any time without having to wait for the exact moment the milk tank is empty. There are neither residual quantities nor times during which the CalfExpert stops feeding due to lack of milk.
The DoubleJug is controlled directly via the CalfExpert. The direct communication between the two devices also has the advantage that the cleaning cycles can be coordinated. The milk line between DoubleJug and CalfExpert is thus only cleaned once a day when the milk tank itself is also cleaned. This minimises the waiting times for the calves.
Conclusion
The highly digestible casein in whole milk ensures high growth rates and prepares the animal for high future performance. In addition, the use of whole milk makes an active contribution to environmental protection because a lot of energy is used for drying and transporting milk replacers.
With a well-thought-out concept, feeding whole milk to calves is no problem. The pasteurisation of milk in the MilkTaxi or FlashPasteur kills germs and ensures safety during feeding. As a modern cooling tank, the DoubleJug is specially adapted to work with calf feeders. As a result, the quality of the milk and the smooth process at the calf feeder are fully guaranteed.